Ford Is Helping Their Disabled and Reduced Mobility Assembly Line Workers by Using Robots to Assist Them
- Production assembly line worker Dietmar Brauner was given a new lease of life in his career at Ford's Cologne plant in Germany by working with a colloborative robot
- The 18-month research project was done to illustrate that disabled people and those with reduced mobility could take on jobs in manufacturing without the need for protective devices or safety barriers
- The robot, called 'Robbie' lines up the holes perfectly in order for Brauner to use an electric screwdriver to secure the covers and the engine moves along the line
PAY ATTENTION: Follow Briefly News on Twitter and never miss the hottest topics! Find us at @brieflyza!
The advent of robots in the manufacturing process usually creates anxiety among the human workforce. Naturally they think their jobs are under threat, but Ford is using robots to assist its diasbled or those with reduced mobilty.
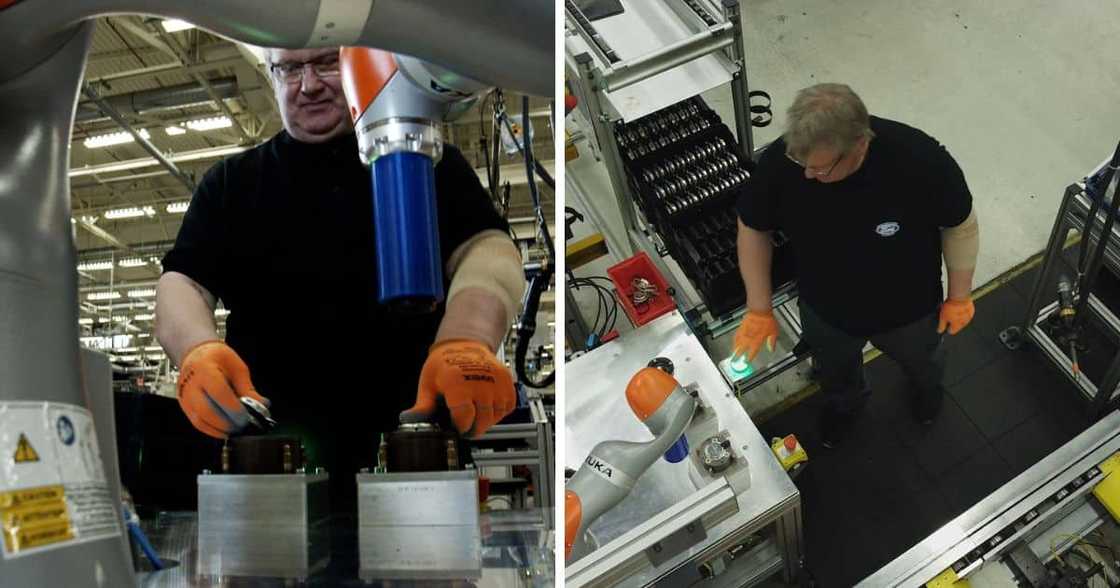
Source: UGC
In a first for the carmaker it has completed an 18-month trial with production line employee Dietmar Brauner a collaborative robot that he has nicknamed Robbie, reports Quickpic. The duo work at the company's assembly line in Cologne, Germany, attaching circular covers to engines.
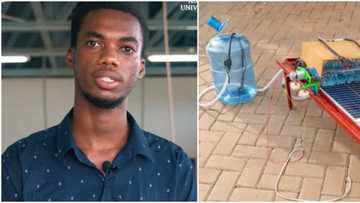
Read also
Innovative African university student builds solar panel that cleans itself of dust without human intervention
According to the Ford Media Centre, Brauner was under the impression his 30-year career was over after recurring health issues led to reduced mobility in his shoulder and wrist.
PAY ATTENTION: Click “See First” under the “Following” tab to see Briefly News on your News Feed!
Instead of Brauner ending his career on the assembly line, Ford joined forces with the RWTH Aachen University and the Landschaftsverband Rheinland (LVR), the largest service provider for disabled people in Germany, which provided €372 000 funding.
The result was an award-winning research project that took 18 months and Robbie the Cobot was working alongside Brauner ton tasks that such employees might otherwise find difficult or impossible.
The project underwent an 18-month trial that was deemed successful and the US carmaker opted to add a new permanent staff member to its plant: 'Robbie'.
What's, even more, encouraging is that the company says the introduction of 'Robbie' could see more cobots used at its production plants around the world.

Read also
'Big Brother Mzansi': Former housemate Tulani 'Tulz' Madala grateful for the overwhelming response to his jersey drive, "Let's make winter warmer"
Dietmar says:
“Over the years, it got harder and harder for me to do my job, Then, along comes this little robot and, for me, it’s like having an extra arm – a very strong extra arm."
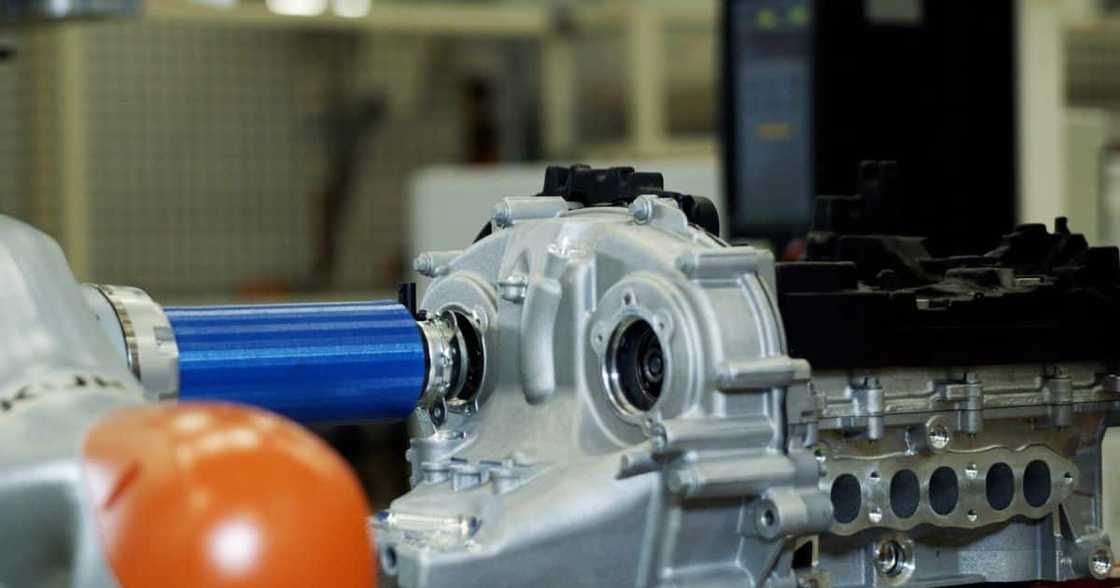
Source: UGC
Brauner uses Robbie to line up the holes perfectly in order for him to use an electric screwdriver to secure the covers and the engine moves along the line.
The robot moves only when activated by Brauner and has sensors that detect when his hands or fingers might be in the way.

Source: UGC
Robots are the future: Ford utilises 3D printers autonomously for optimal efficiency and lower cost
Javier is the name of Ford's robot at its Advanced Manufacturing Centre and operates the 3D printers autonomously, Briefly News reports.
This innovative robot on wheels from supplier KUKA is integral to the company’s development of an industry-first process to operate 3D Carbon printers with an autonomous mobile robot.
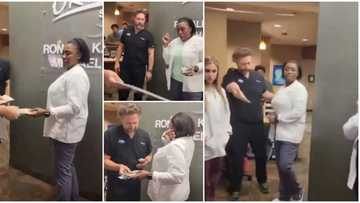
Read also
Woman gets over R300k on the spot from her Oyinbo bosses for being a loyal employee, video melts hearts
Typically, different pieces of equipment from various suppliers are unable to interact because they do not run the same communication interface, Ford says in a blog post. Ford developed an application interface programme that allows different pieces of equipment to “speak the same language” and send constant feedback to each other.
PAY ATTENTION: check out news exactly for YOU ➡️ find "Recommended for you" block and enjoy!
Source: Briefly News